WHAT IS STAINLESS STEEL ?
About Stainless Steel We have all hear of stainless steel but when you ask people what it actually is they are often unable to answer. Effectively stainless steel whether in stainless steel sheets, stainless steel wire or other stainless steel products it is a low carbon steel which contains chromium at 10% or more by weight about Stainless Steel.
It is the addition of the chromium to the carbon steel which gives it the ability to be able to resist corrosion. However, it is far more amazing than that because if becomes damaged mechanically or chemically then it has a film which is self healing proving oxygen is present.
The more chromium which is present within the low carbon steel then the more properties such as the above are increased. These properties can be enhanced further when other elements are added and a prime example of this is molybdenum, nickel and nitrogen.
Why Use Stainless Steel?
One of the main reasons why people choose to use stainless steel is because of its advantages and physical properties, the most popular is its corrosion resistance although there are many more.
The fact that it has such a resistance to high and low temperatures means that stainless steel can be used for a number of applications and throughout a number of industries. Whilst some stainless steel will retain high strength at high temperatures other stainless steels will actually maintain high mechanical properties at cryogenic temperatures.
A major reason that stainless steel is used is because of its sheer strength. This has been proven through its use in the building and construction industry. The aesthetic appeal which stainless steel has makes it a popular choice for many. Stainless steel is available in a range of surface finishes and the fact that it can also be polished makes it aesthetically pleasing to the eye.
Its long life cycle makes it perfect for use in buildings and puts it ahead of other products in the fact that it will outlast many of them. When you add in that stainless steel is easy to maintain and put these reasons together overall it is the lowest cost choice for many in a life cycle cost comparison.
About Stainless Steel As it is an environmentally friendly material because it is 100% recyclable any new stainless steel normally contains around 50-80% recycled material. Stainless steel is undoubtedly a valuable material which has many uses within a whole range of industries and without it we would have to use other materials which wouldn’t be as effective.
If you require stainless steel for whatever reason then contact Matrix metal Alloys. We are the independent supplier of stainless steel products and can offer a full range as well as a brilliant service to our customers.
Stainless steel is a family of iron-based alloys that contain a minimum of approximately 11% chromium, a composition that prevents the iron from rusting, as well as providing heat-resistant properties. Different types of stainless steel include the elements carbon (from 0.03% to greater than 1.00%), nitrogen, aluminium, silicon, sulfur, titanium, nickel, copper, selenium, niobium, and molybdenum. Specific types of stainless steel are often designated by a three-digit number, e.g., 304 stainless.
Stainless steel resistance to ferric oxide formation results from the presence of chromium in the alloy, which forms a passive film that protects the underlying material from corrosion attack, and can self-heal in the presence of oxygen. Corrosion resistance can be increased further, by increasing the chromium content to levels above 11%; addition of 8% or higher amounts of nickel; and
addition of molybdenum (which also improves resistance to “pitting corrosion”).
The addition of nitrogen also improves resistance to pitting corrosion and increases mechanical strength.[5] Thus, there are numerous grades of stainless steel with varying chromium and molybdenum contents to suit the environment the alloy must endure. Resistance to corrosion and staining, low maintenance, and familiar luster make stainless steel an ideal material for many applications where both the strength of steel and corrosion resistance are required. About Stainless Steel Moreover, stainless steel can be rolled into sheets, plates, bars, wire, and tubing.
These can be used in cookware, cutlery, surgical instruments, major appliances, construction material in large buildings, industrial equipment (e.g., in paper mills, chemical plants, water treatment), and storage tanks and tankers for chemicals and food products. The material’s corrosion resistance, the ease with which it can be steam-cleaned and sterilized, and the absence of the need for surface coatings have prompted the use of stainless steel in kitchens and food processing plants.
About Stainless Steel Austenitic stainless steel Main article: Austenitic stainless steel Austenitic stainless steel is the largest family of stainless steels, making up about two-thirds of all stainless steel production (see production figures below).[32] They possess an austenitic microstructure, which is a face-centered cubic crystal structure.[33] This microstructure is achieved by alloying steel with sufficient nickel and/or manganese and nitrogen to maintain an austenitic microstructure at all temperatures, ranging from the cryogenic region to the melting point.[33] Thus, austenitic stainless steels are not hardenable by heat treatment since they possess the same microstructure at all temperatures.
Austenitic stainless steels can be further subdivided into two sub-groups, 200 series and 300 series: 200 series are chromium-manganese-nickel alloys that maximize the use of manganese and nitrogen to minimize the use of nickel. Due to their nitrogen addition, they possess approximately 50% higher yield strength than 300 series stainless sheets of steel.
About Stainless Steel Type 201 is hardenable through cold working.[citation needed] Type 202 is a general-purpose stainless steel. Decreasing nickel content and increasing manganese results in weak corrosion resistance. 300 series are chromium-nickel alloys that achieve their austenitic microstructure almost exclusively by nickel alloying; some very highly-alloyed grades include some nitrogen to reduce nickel requirements. 300 series is the largest group and the most widely used.
Type 304: The best-known grade is Type 304, also known as 18/8 and 18/10 for its composition of 18% chromium and 8%/10% nickel, respectively.[citation needed] Type 316: The second most common austenitic stainless steel is Type 316. The addition of 2% molybdenum provides greater resistance to acids and localized corrosion caused by chloride ions. Low-carbon versions, such as 316L or 304L, have carbon contents below 0.03% and are used to avoid corrosion problems caused by welding.
Ferritic stainless steels Main article: Ferritic stainless steel Ferritic stainless steels possess a ferrite microstructure like carbon steel, which is a body-centered cubic crystal structure, and contain between 10.5% and 27% chromium with very little or no nickel. This microstructure is present at all temperatures due to the chromium addition, so they are not hardenable by heat treatment. They cannot be strengthened by cold work to the same degree as austenitic stainless steels.
They are magnetic. Additions of niobium (Nb), titanium (Ti), and zirconium (Zr) to Type 430 allow good weldability (see welding section below). Due to the near-absence of nickel, they are cheaper than austenitic steels and are present in many products, which include:Automobile exhaust pipes (Type 409 and 409 Cb[2] are used in North America; stabilized grades Type 439 and 441 are used in Europe).
Architectural and structural applications (Type 430, which contains 17% Cr)[38] Building components, such as slate hooks, roofing, and chimney ducts Power plates in solid oxide fuel cells operating at temperatures around 700 °C (1,292 °F) (high-chromium ferritic containing 22% Cr)[39] Martensitic stainless steels Main article: Martensitic stainless steel Martensitic stainless steels offer a wide range of properties and are used as stainless engineering steels, stainless tool steels, and creep-resistant steels. They are magnetic, and not as corrosion-resistant as ferritic and austenitic stainless steels due to their low chromium content. They fall into four categories (with some overlap):[40]
Fe-Cr-C grades. These were the first grades used and are still widely used in engineering and wear-resistant applications. Fe-Cr-Ni-C grades. Some carbon is replaced by nickel. They offer higher toughness and higher corrosion resistance. Grade EN 1.4303 (Casting grade CA6NM) with 13% Cr and 4% Ni is used for most Pelton, Kaplan, and Francis turbines in hydroelectric power plants[41] because it has good casting properties, good weldability and good resistance to cavitation erosion. Precipitation hardening grades. Grade EN 1.4542 (also known as 17/4PH), the best-known grade, combines martensitic hardening and precipitation hardening.
It achieves high strength and good toughness and is used in aerospace among other applications. Creep-resisting grades. Small additions of niobium, vanadium, boron, and cobalt increase the strength and creep resistance up to about 650 °C (1,202 °F). Heat treatment of martensitic stainless steels Martensitic stainless steels can be heat treated to provide better mechanical properties.The heat treatment typically involves three steps:[42]
Austenitizing, in which the steel is heated to a temperature in the range 980–1,050 °C (1,800–1,920 °F), depending on grade. About Stainless Steel the resulting austenite has a face-centered cubic crystal structure. Quenching. The austenite is transformed into martensite, a hard body-centered tetragonal crystal structure. The quenched martensite is very hard and too brittle for most applications. Some residual austenite may remain. Tempering. Martensite is heated to around 500 °C (932 °F), held at temperature, then air-cooled. Higher tempering temperatures decrease yield strength and ultimate tensile strength but increase the elongation and impact resistance.
Nitrogen-alloyed martensitic stainless steels Replacing some carbon in martensitic stainless steels by nitrogen is a recent development, The limited solubility of nitrogen is increased by the pressure electroslag refining (PESR) process, in which melting is carried out under high nitrogen pressure. Steel containing up to 0.4% nitrogen has been achieved, leading to higher hardness and strength and higher corrosion resistance. About Stainless Steel As PESR is expensive, lower but significant nitrogen contents have been achieved using the standard argon oxygen decarburization (AOD) process.
Duplex stainless steel Main article: Duplex stainless steel Duplex stainless steels have a mixed microstructure of austenite and ferrite, the ideal ratio being a 50:50 mix, though commercial alloys may have ratios of 40:60. They are characterized by higher chromium (19–32%) and molybdenum (up to 5%) and lower nickel contents than austenitic stainless steels. Duplex stainless steels have roughly twice the yield strength of austenitic stainless steel. Their mixed microstructure provides improved resistance to chloride stress corrosion cracking in comparison to austenitic stainless steel Types 304 and 316.
Duplex grades are usually divided into three sub-groups based on their corrosion resistance: lean duplex, standard duplex, and super duplex.
The properties of duplex stainless steels are achieved with an overall lower alloy content than similar-performing super-austenitic grades, making their use cost-effective for many applications. The pulp and paper industry was one of the first to extensively use duplex stainless steel.
About Stainless Steel Today, the oil and gas industry are the largest user and has pushed for more corrosion resistant grades, leading to the development of super duplex and hyper duplex grades. More recently, the less expensive (and slightly less corrosion-resistant) lean duplex has been developed, chiefly for structural applications in building and construction (concrete reinforcing bars, plates for bridges, coastal works) and in the water industry.
Precipitation hardening stainless steels Precipitation hardening stainless steels have corrosion resistance comparable to austenitic varieties, but can be precipitation hardened to even higher strengths than other martensitic grades. There are three types of precipitation hardening stainless steels:[48]
Martensitic 17-4 PH (AISI 630 EN 1.4542) contains about 17% Cr, 4% Ni, 4% Cu, and 0.3% Nb. Solution treatment at about 1,040 °C (1,900 °F)followed by quenching results in a relatively ductile martensitic structure. Subsequent aging treatment at 475 °C (887 °F) precipitates Nb and Cu-rich phases that increase the strength up to above 1000 MPa yield strength. This outstanding strength level is used in high-tech applications such as aerospace (usually after remelting to eliminate non-metallic inclusions, which increases fatigue life). Another major advantage of this steel is that aging, unlike tempering treatments, is carried out at a temperature that can be applied to (nearly) finished parts without distortion and discoloration.
Semi-austenitic 17-7PH[49] (AISI 631 EN 1.4568) contains about 17% Cr, 7.2% Ni, and 1.2% Al. About Stainless Steel Typical heat treatment involves solution treatment and quenching. At this point, the structure remains austenitic. Martensitic transformation is then obtained either by a cryogenic treatment at −75 °C (−103 °F) or by severe cold work (over 70% deformation, usually by cold rolling or wire drawing).
Aging at 510 °C (950 °F)—which precipitates the Ni3Al intermetallic phase—is carried out as above on nearly finished parts. About Stainless Steel Yield stress levels above 1400 MPa are then reached.Austenitic A286[50](ASTM 660 EN 1.4980) contains about Cr 15%, Ni 25%, Ti 2.1%, Mo 1.2%, V 1.3%, and B 0.005%. About Stainless Steel The structure remains austenitic at all temperatures.
Typical heat treatment involves solution treatment and quenching, followed by aging at 715 °C (1,319 °F). About Stainless Steel Aging forms Ni3Ti precipitates and increases the yield strength to about 650 MPa at room temperature. Unlike the above grades, the mechanical properties and creep resistance of this steel remain very good at temperatures up to 700 °C (1,292 °F). As a result, A286 is classified as an Fe-based superalloy, used in jet engines, gas turbines, and turbo parts.
For more information call us on +91 9499949357 or email [email protected]
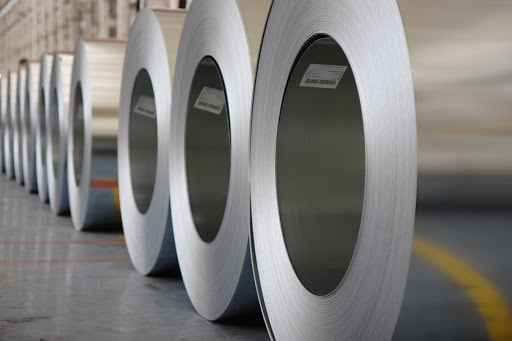